GreenZyme® single well booster treatment
​
Treatments are usually very simple to implement (product, equipment, people) and can be completed in a single day. Most Huff n Puff crude oil recovery treatments to date have used GreenZyme® concentrate diluted to solutions between 2%-10% strengths with over 90% success rate world wide in improving production.
The enzyme concentrate is mixed with available and reservoir compatible water at the site to then be pump down the well using traditional injection methods (for example: bullheading, coiled tubing). The objective is to displace the solution into the oil producing zone. Bullheading is a common and cost effective methodology for implementation.
Once GreenZyme® molecules enter the zone to be treated, it further uses the reservoir and water available as a mixing tank, continuing to diffuse further in the layer. Additional formation water is injected from surface to clear the premium fluid from the injection tube and to displace the remaining fluid into the formation. Making contact with the rock it creates a oil-repelling surface (positive enzyme-water skin) that will prevent re-attachment of crude oil while helping improve drainage and relative permeabilities of the reservoir.
​
Water based enzyme detergent solution can also be pre-heated at the time of well treatment injection to 80C degrees to avoid pour point issues, and has been recorded active and working to separate oil at to 270 C (450 C under reservoir pressure) in laboratory surface testing.
​
Water based additive compatible with multiple oil well intervention tactics, different well profiles and field challenges.
​
Once pumping is completed, the well is soaked for 3-5 days to give the enzyme fluid time to diffuse in the producing layer, promoting changes in wettability by the creation of the enzyme-water positive skin on the rock surface. GreenZyme molecules will produce a change of adhesion behavior of hydrocarbons that will increase reservoir fluid mobility and crude oil recovery.
​
Like a detergent, the result of using GreenZyme® in any reservoir is increased permeation and drainage of the reservoir fluid by washing away of oil from rock.
After soaking time, open well and bring back to production over time and monitor metrics for for the best crude oil recovery results.
​
Buy, Ship, Implement and get recorded Results in 90 days!
Effective and proven solution for:
Heavy Oil fingering and water cone mitigation, emulsion dispersant,
slow and unproduced oil pockets, new wells with rapid decline in productivity.
​4 Hour work, results by 30 days​
-
Oil production enhancer Huff-n-Puff
-
Water based enzyme concentrate oil washing additive
-
Mix detergent concentrate with available field water
-
Implement with: 1) mix tank and 2) pump equipment
-
Displace solution into production zone
-
Displace additional water, close and then Soak
-
Re-start & Recover
Compatible with:
Vertical, Horizontal & Off-shore wells​
-
Huff n Puff, Heavy oil, fingering, water cone
-
Waterflooding & Cluster Floods
-
WAG, Steam & SAGD pre-soak
Implemented using: ​
-
Surface injection pumps / mix truck
-
Coiled Tubing equipment
-
Bullheading, casing..
-
with completion fluids
GreenZyme® Smart Water Additive
​
The water based Enzyme Fluid Technology is a perfect additive to any oil separation water process operation. GreenZyme® is designed as a hydrocarbon separator that turns water into a powerful detergent surfactant that dissipates crude oil from any surface improving crude oil well recovery factors using environmentally friendly solutions.
​
It can easily be used in reservoir oil production when mixed and dosed into active injection water drive. Enzyme Enhanced Oil Recovery (EEOR) treatments have shown the use of enzyme detergent can decrease injection pressure of the water drive, increase capacity of the formation to receive water, improve sweep efficiency and volume recovery.
​
GreenZyme® penetrates the pores to displace crude oil.
Biologically and batch made yet inert, GreenZyme® is not a solvent and does not react with other chemicals, the crude oil, nor the rock. Positive effect of enzyme fluid is that it interferes with the attachment of crude oil to the rock surface, as well as influencing the attachment of crude oil to itself. GreenZyme® polar activity behaves like an electrolyte, and has the ability to perform oil liberation in high and low salinity environments.
GreenZyme® has been found to be a very effective way to pre-soak in the well for Steam and SAGD cycles as the temperature also increases the vibration of crude molecules, creating a synergy that makes crude more mobile. Enzyme molecules adsorbed to the rock surface do not denature with temperature, therefore will promote crude mobility creating non-attachment enzyme-water skin in the drainage zone.
The synergy beneficial created when enzyme technology penetrates and diffuses in the formation changing the attachment behavior of oil, improving permeability and fluid mobility in the reservoir at the time that is sweeped by the Steam. Optimization report have shown 25% to 50% less steam is required for Steam Cycle with an incremental increase in recovery.
GreenZyme® for waterflood & Clusters
​
The GreenZyme® Enhanced Oil Recovery (EEOR or GEOR) fluid technology can be, batch dosed, slugged or injected sporadically in a waterflooding to improve the conditions of the sweep. When reaching the formation, start cleaning to allow for more water intake as it diffuses into the layer connectivity. GreenZyme treatments are known to influence near by oil wells about 150 meters away when used in simple huff and puff implementations. Monitoring near by wells is advised.
Pumping batches GreenZyme® into injector wells is a simple procedure and does not require continuous non stop use. Given the limits that currently exist for recovery technologies, treatment with enzyme fluid solution is reliable and cost effective way to achieve improved oil recovery, including at heavy API gravity oil.
Clusters can be treated from central injector to produce a multi-well effect, which creates the opportunity to use less product to reach more wells when taking into account connected and continuos reservoir pay zones. GreenZyme® molecule is highly diffusible in water and will travel in the layer seeking attachment to oil, cleaning and mobilizing crude oil in its path.
Submit a question directly to Oil Well Solutions Team
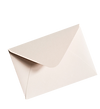


Container & packing
Container & Packing: KEEP INDOORS, AWAY FROM THE SUN!
-
220 gallon IBC tote with integrated pallet
-
55gal drum + wood pallet (4 drums per pallet)
-
​
Cargo is inspected before it boards the shipping container:
• IBC or Drum & Pallet Integrity.
• Sealed Top Cap with additional tamper evident seals
• Steel Strapping for drums, steel cage for IBC protection
• Secured Bottom IBC Valve with tamper evident seal
​
Quality Control & Inventory Tracking to each individual country:
• Proper Import - Export labeling is attached to each Drum or IBC.
• Each Drum or IBC of GreenZyme® carries a Unique Numbered Security Identification Label specific to each Country or Territory
​
Certificate of Shipping, Transport & Free Trade Agreements:
• Shipping Container Number
• Quality Control Identification Label Numbers
• Shipping Container Metallic Seal Number
• Project Name and Destination
​
LOGISTICS
Biotech Processing Supply works with agents and Oil Field operators to arrange project Evaluation, Engineering, Promotion, Trade, Distribution, Shipment and Implementation of GreenZyme® Technology
​
Most of our orders ship in 20’ or 40’ containers using FOB or CIF modality for international shipping, flat bed trucks for distribution in the Continental USA to client or Forwarding agent.
​